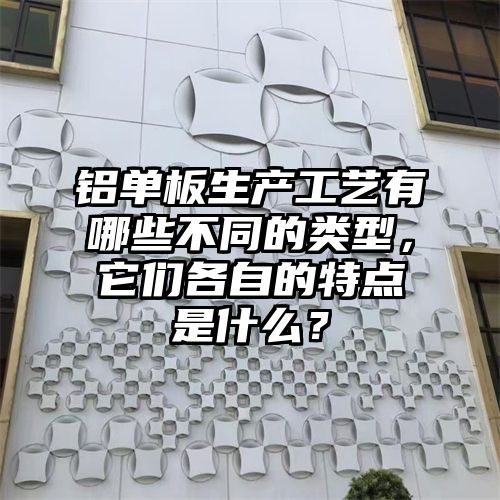
What are the different types of aluminum veneer production processes and their respective characteristics?
Abstract: This article will provide a detailed introduction to the different types of aluminum veneer production processes, including hydraulic forming, mechanical forming, extrusion forming, and spray forming, and explain their respective characteristics and advantages.
1、 Hydraulic forming
Hydraulic forming is a common process type in the production of aluminum veneer. This process uses hydraulic pressure to process aluminum plates into the desired shape. The characteristics of hydraulic forming include the following aspects: 1 High precision: Hydraulic forming can precisely control the shape and size of the machining according to the requirements, ensuring the accuracy and consistency of the product. 2. Fast molding speed: Hydraulic molding has a fast working speed, which can meet the needs of large-scale production and improve production efficiency. 3. Low cost: Hydraulic equipment is relatively simple and cost-effective, suitable for production in small and medium-sized enterprises.
2、 Mechanical Forming
Mechanical forming is a type of process that uses mechanical force to shape aluminum plates. Compared with hydraulic forming, mechanical forming has the following characteristics: 1 Strong flexibility: Mechanical molding can achieve different shapes of processing by changing molds, suitable for diverse product needs. 2. High production efficiency: Mechanical forming equipment operates stably and has a high degree of automation, which can improve production efficiency and output. 3. High cost: The price of mechanical forming equipment is relatively high, and for larger enterprises, the investment cost is high.
3、 Extrusion molding
Extrusion molding is a process of heating aluminum material to a molten state and forming the desired cross-sectional shape through an extrusion mold. The characteristics of extrusion molding are as follows: 1 High product precision: Extrusion molding can achieve complex cross-sectional shapes, resulting in high product precision and good surface smoothness. 2. Material saving: Extrusion molding can reduce material waste, improve material utilization, and reduce production costs. 3. Wide applicability: Extrusion molding is suitable for the production of aluminum products with various cross-sectional shapes and has a wide range of applications.
4、 Spray molding
Spray forming is a type of process that involves spraying coatings onto the surface of aluminum plates. The characteristics of this process are as follows: 1 Colorful: Spray molding can spray various colors of coatings according to needs, meeting different styles and decorative requirements. 2. Surface protection: Spray formed coatings can provide protection for the surface of aluminum plates, increasing the product's weather resistance and corrosion resistance. 3. Personalized design: Spray molding can achieve personalized customization by designing different patterns and textures to meet customers' special needs.
5、 Summary:
In summary, the production process of aluminum veneer includes different types such as hydraulic forming, mechanical forming, extrusion forming, and spray forming. Each process has its unique characteristics and advantages, and hydraulic forming has the advantages of high precision, fast forming speed, and low cost; Mechanical forming has the characteristics of strong flexibility, high production efficiency, and high cost; Extrusion molding has the advantages of high product accuracy, material savings, and wide applicability; Spray molding has the characteristics of rich color, surface protection, and personalized design. Different types of processes can choose suitable methods based on demand and product requirements to improve production efficiency and product quality.